Who am I?
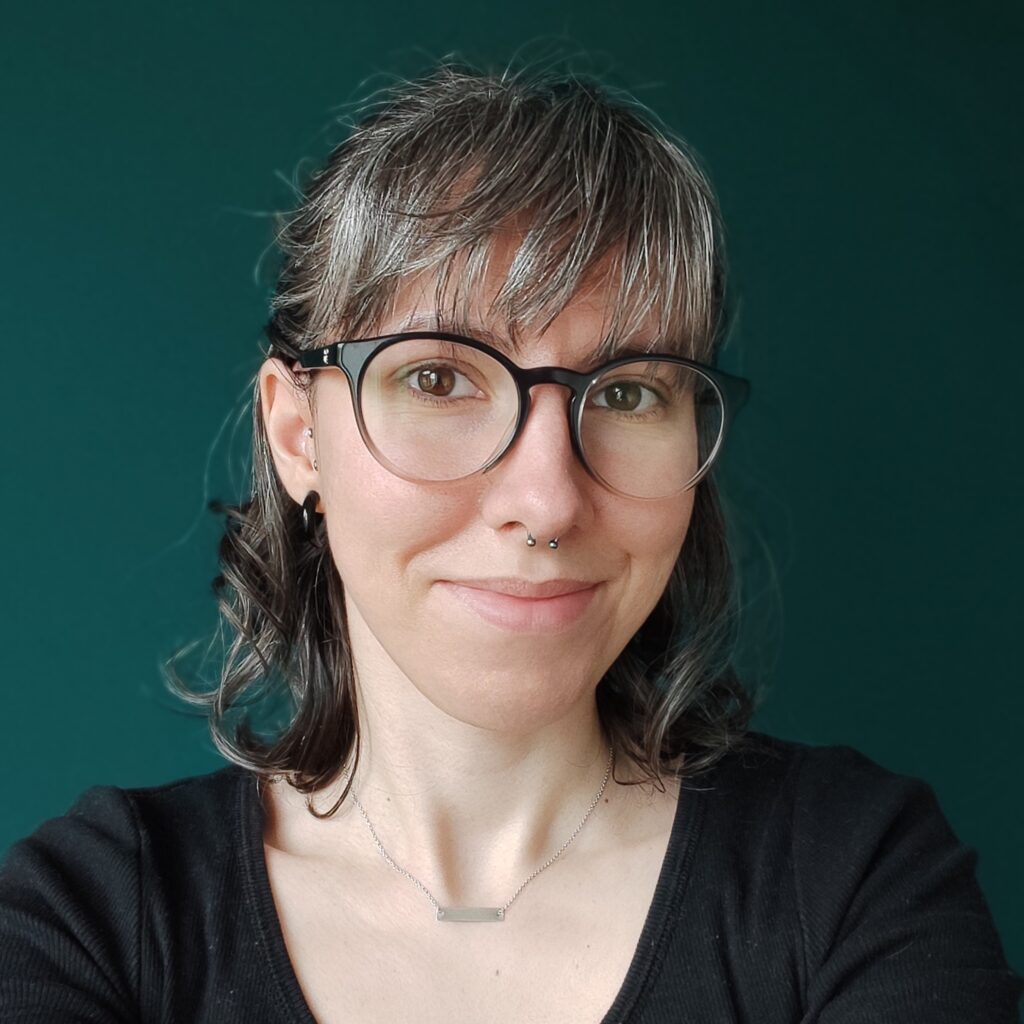
My name is Magdalena Walaszek, I have woven my first scarf in 2020. You can find me in social media as MAVA Loom. An architect by training, wife of a wounderful husband, mom of a little tornado and a cat mom of two night furies. I like board games, films, analogue photographs, cuddling cats and coffee with cake.
Since I first came to the weaving world, it never stops to amaze me. What I love about it, is that it engages various senses. I can touch each texture, see how the yarn absorbes the dyes, the colours mix and blend, feel the smell. But what I think I love the most, is that weaving combines beauty and utility, each wrap lives its own life and every textile that came of the loom can be used.
I find inspiration everywhere, there’s not a single day that I don’t imagine how something I have just seen would look like on my loom. I like to create concepts, in which every thread is there for a reason and the wrap tells a story with a beginning and an ending. And sometimes I just like to play with weaving, texture and yarn.
What I do?
I handweave on a multi-shaft loom as well as hand dye the yarn I use for weaving. The process takes a lot of time and patience, as I start my work with raw, natty yarn to make it into the final scarf or shawl that will wrap you up.
Each warp, that means threads, that I wind on the loom, is made from undyed natural yarn, which I am winding, that is, I measure the right amount and length of thread. The warp, depending on whether it is for scarves or shawls and slings, can have between 400 and even 1,000 threads, each thread at least a few metres long, making many kilometres of yarn, all of which passes through my fingers first, as measuring the warp is also a manual job.
Once I have measured the correct amount and length of thread, I move on to the next stage of the work, the dyeing. I use high-quality textile dyes, which only require commonly available and environmentally safe reagents. The dyeing process makes each fabric unique, as it is not possible to replicate the exact colour distribution or achieve the same shades every time, so you can be sure that your product is one of a kind.
Once the warp is dyed, it is time to put it on the loom. Once wound on the loom, each of the warp threads must be threaded through the heddles properly to create the patterns that are on your fabrics. Yes, each of the hundreds of threads separately. And then a second time, through the so-called reed. Once all the threads are in place, you can move on to preparing the wefts and to the main part - weaving!
At this point, the fabric is formed. The weft, or cross thread, is inserted between the warp threads, one by one, thread by thread, thousands of times, until the desired length is reached. Once the desired length is woven, I cut the finished fabric from the rest of the warp and do the final touches.